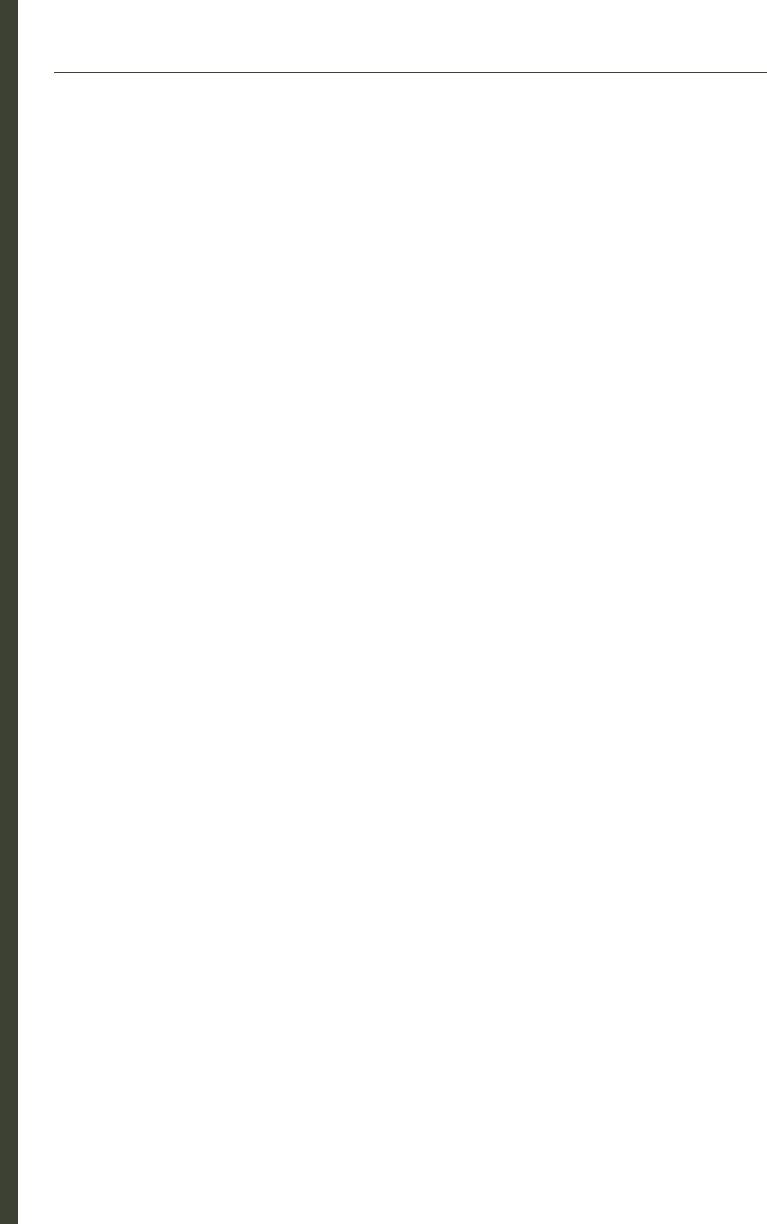
136
GLOSSARY
Insulation, berglass: Type of insulation,
composed of small diameter glass bers,
formed into blankets or batts, or used in
loose-ll and blown-in applications.
Insulation, ash and batt: Insulation method
for exterior walls where cavities are lled
with a combination of spray foam and batt
insulation. Using higher R-value and air
sealing foam creates a better building, and
using less expensive batt insulation at the
interior face of the cavity saves money.
Insulation, foam: High R-value insulation
product made from a variety of plastic
materials (polyurethane, polystyrene,
extruded polystyrene, expanded
polystyrene, polyisocyanurate). Available
in boards or spray onto roofs, oors, rim
joists, and gaps such as at penetrations
and window and door frames. A less
common application is injection into
closed wall or oor cavities. R-value,
expansion rates, permeability, and setting
times vary by material.
Insulation, loose ll: Insulation made from
berglass, cellulose, or other materials
composed of loose bers or granules,
which can be applied by pouring directly
from the bag or with a blower unit.
Insulation, rigid board: Plastic foam
insulation product, pressed or extruded;
typically used as insulation for interior
basement or crawl space walls, beneath
basement or crawl space slabs, and at
exterior below-grade or above-grade
walls. Panel dimensions and thicknesses
vary. R-values typically range from 3.2 to
7 per inch. At exterior walls, it can provide
contiguous insulation that creates the
building thermal envelope (foundation,
exterior walls, and roof).
Insulation, spray foam: Foam insulation
(open cell/low density or closed cell/
high density) for spray application and/or
injection into closed cavities. Installation
includes mixing of polyurethane resin
with a blowing agent using specialized
equipment, causing foam to expand to ll
cavity and encapsulate tiny gas cavities.
Must be separated from the interior of a
building by an approved thermal barrier
or approved nish material unless rated for
exposure. A less common application is
injection into closed wall or oor cavities.
Insulation, spray foam-open cell: Open
or low density foam (approximately
.5 lb/ft
3
) that is sprayed or injected.
R-value approximately 3.6 per inch.
One advantage of open cell spray foam
is that alternate blowing agents with
less adverse environmental impact and
greater durability are available. Considered
an air barrier. when minimum thickness is
5 inches.
Insulation, spray foam-closed cell: Closed
or high density foam (approximately
2.0 lb/ft
3
) that is sprayed or injected.
R-value approximately 6.0/inch, although
decreases over time as air replaces
hydrocarbon gas used as the blowing
agent. Considered an air barrier; has good
adhesion and structural strength.
Light pollution: Excessive articial light
from a building site that exceeds occupant
needs and produces glare.